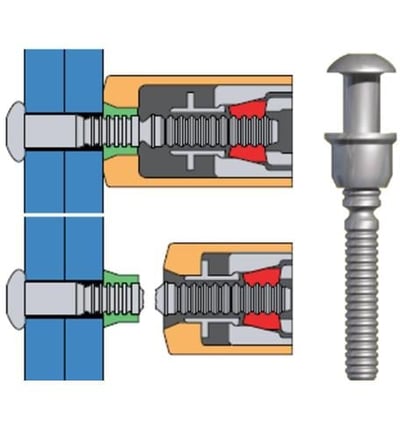
Throughout the history of mechanical construction, there has always been a need for a completely permanent fastening system—one that essentially becomes a part of the piece on which it is used. Welding two objects together is one such fastening method, but it requires expert installers using high temperatures, gases, and heavy protective equipment, all of which make it difficult to accomplish, especially in hard-to-reach locations.
The need for a simple-to-install yet permanent fastener was finally met in 1944, when Louis C. Huck sketched the first vibration-resistant lockbolt for use on rails and railcars. The HuckBolt® brand later became part of Alcoa Fastening Systems, now known as Arconic Fastening Systems.
Today, Huck bolts are made out of a variety of materials, with many different styles for specific applications. Huck fasteners are most often used in manufacturing, mining equipment, shipbuilding, and agriculture, as well as in trucks, trailers, bridges, railways, and railcars, where vibration is ever-present.
The Benefits of the Huck Bolt
Threaded fasteners have been around for centuries and are extremely useful for a wide range of applications. The only problem is that threaded fasteners such as nuts and bolts can work loose over time, especially if they are being used for high-stress applications or where continuous vibration is a problem. The Huck bolt was developed to solve that problem by completely redesigning the bolt as a two-piece fastener that uses metal-on-metal contact to secure it in place as a permanent bond.
The Huck bolt consists of two pieces: a threaded pin and a collar made of slightly softer material. Huck bolts are available in different sizes and materials for different applications:
- The Huck BobTail® is corrosion-resistant, can be installed using a lightweight tool, and is available in steel, stainless steel, and aluminum.
- The C50L® is designed for heavy-duty applications, meets or exceeds the ASTM A-325 standards for shear and tensile strength, and is available in steel, stainless steel, or aluminum.
- The Magna-Grip® is a vibration-resistant grade 2 fastener with a wide grip range, and it is available in steel and aluminum.
- Designed for a broad range of applications, the C6L, C120L, and C150L Huck bolts feature classic, six-groove fastening and are available in steel, stainless steel, aluminum, and as steel pins with stainless steel heads.
- Arconic also offers the Hucktainer® steel fastener, designed to be installed with consistent pressure for working with softer materials without crushing them.
When installed, the pin is inserted into one side of the workpiece and the collar is fitted on the opposite side, then tightened using a rivet tool that swages the collar to the pin to form a permanent bond. Huck bolts come in three basic designs: the Huck bolt with a pintail that remains after installation, the Huck bolt whose pintail is broken off during installation, and the reinforced-panel Huck bolt for use with softer materials.
Key Things to Know About Huck Bolts
1. Alternative to Nuts and Bolts
The original Huck lockbolt was designed to be an alternative to a threaded fastener consisting of a nut and a bolt. The new two-piece clamping fastener was ideal for a variety of locking applications that required high uniform clamp force and vibration resistance.
2. Extremely High Vibration Resistance
The original Huck bolt design resisted vibration like that experienced on rails and railway cars. Because vibration causes threaded fasteners to lose clamp force due to the shear load, typically they require periodic retightening—a maintenance headache and, in some cases, a threat to safety.
Unlike threaded nuts and bolts, Huck lockbolts allow no relative movement between the cylindrical collar and a threaded pin. At installation, the smooth collar is permanently swaged or deformed into place over the pin’s lock grooves. The result is labor cost savings and a safer joint.
3. Permanent Fastened Joint
Compared with conventional nut-and-bolt fasteners, the Huck lockbolt is a permanent, high-strength joint. A Huck lockbolt has a larger cross-sectional area and core diameter than a bolt of the same size, providing 10-20 percent greater tensile strength, according to Arconic, the maker of Huck bolts.
4. Simplified Installation
Huck lockbolts are easy to install in seconds using the special Huck tooling system. The tools, which must be matched to the fastener’s particular size, use either pneumatic or hydraulic power to swage the collar over the pin. The tools can be operated with minimal training—no expertise is required.
5. Faster Installation
Simple installation means reduced installation time—25-50 percent faster than conventional threaded nut-and-bolt fasteners when using the Huck U-Spin tools. Huck’s line of POWERIG power units, including heavy-duty hydraulic installation tools, make for fast and easy assembly of large quantities of lockbolts, with reduced costs.
7 Reasons to Use HuckBolts® Over Welds
At one time, welding was the most reliable and common way to secure joints in load-bearing structures that endure high levels of vibration. However, in most industrial applications today, welding isn’t practical—or safe. Here are seven ways swaged-on, direct-tension lockbolts, such as HuckBolts®, are taking the place of welds.
1. They Ensure Safety
With welding, there is always the danger that a random spark will start a fire, making welding much more dangerous than HuckBolts® in implementation. Additionally, spent rods and other materials can become safety hazards on the production floor. These spent materials can also interfere with the organization and cleanliness of your worksite. Welding also comes with countless health risks, such as lung cancer, retina damage, asthma, and more. Using HuckBolts®, you avoid the dangers that come with welding.
2. You Can Install Them Quickly
Welding—especially complicated welds—takes time, which impacts production time. HuckBolts® offer fast, reliable installation. With welds, your materials have to be spotless prior to joining, but with HuckBolts®, this isn’t necessary. They’re incredibly easy to install without any special tooling, and the best part? You avoid the human error that often comes along with welding.
3. They Are Immune to HAZ
With HuckBolts®, you don’t have to worry about the impact of heat-affected zones (HAZ), which is when the space between the melted area and the unaffected base metal experiences chemical and structural modifications. HAZ can weaken the materials, cause corrosion, and damage critical surface coatings. With HuckBolts®, you avoid HAZ and ensure the integrity of your workpiece.
4. They Can Be Inspected Regularly
HuckBolts® allow for quick inspection, whereas welds are difficult to inspect and the inspections often require expensive equipment. In many cases, welds don’t get inspected at all, which can be a major safety hazard.
5. They Ensure Integrity
Avoid weld fatigue! HuckBolts® ensure a high level of vibration resistance, which means a solid joint that can withstand years of use. HuckBolts® are also built to avoid the problems of thermal expansion experienced with welds, which can damage the integrity of the workpiece.
6. You Can Modify Them Easily
Another great advantage of using HuckBolts® is that they are easy to rework or remove from an application. Welds, on the other hand, are extremely difficult and time-consuming to try and rework once the weld is set. Thus, HuckBolts® provide greater flexibility and will save you money in the long run.
7. You Can Save Money
Installing HuckBolts® requires little to no experience, which means you don’t have to hire costly specialists and supervisors for the job. All the operator needs to do is complete a quick inspection of the bolt installation to verify the joint is solid. Welding is also more costly because you need to have expensive ventilation systems to remove harmful gases, not to mention special aprons, gloves, and masks.
The Huck Bolt Installation Sequence
The basic installation procedure is the same for all Huck bolt types.
- Determine the right Huck bolt for the application. You want to choose a Huck bolt that has the right tensile strength, size, and other properties for the application.
- Fit the Huck bolt pin in the pre-drilled hole. The pin diameter should match the hole size for a tight fit to prevent lateral movement that could weaken the joint.
- Fit the Huck bolt collar on the side opposite from the pinhead. The collar fits over the pin and will form a strong, lasting joint when the collar is swaged using a riveting tool.
- Place the nosepiece of the riveting tool over the pintail and into the collar and activate the tool. The pressure applied to the collar simultaneously pulls on the pintail to bring the pieces being joined together and swages the collar to maximize metal-on-metal contact so, unlike a nut and bolt, it cannot work loose. The tensile strength of the Huck bolt is dictated by the number of grooves that are filled.
- The tool breaks off the pintail and installation is complete.
After you have completed these five steps, a quick visual inspection should tell you whether you have installed the Huck bolt correctly.
There are some variations to this procedure, depending on the installation and Huck bolt type. For example, some rivet tools will collect the spent pin to minimize hazards and cleanup. Also, some Huck bolts are designed to leave the pintail intact, so it doesn’t have to be removed. There also are a variety of Huck bolt tools to choose from, including pneudraulic installation tools, hydraulic installation tools, and battery-operated tools, depending on the application.
This blog was originally published in February 2018 and updated in August 2020.
Comments